Die Geschichte des Eames Plastic Shell Stuhls begann schon mehr als zehn Jahre vor dem Debüt von Charles und Ray Eames im Jahr 1950 mit ihrem inzwischen ikonischen Design für Herman Miller. Sich diese mehr als ein Jahrzehnt dauernde Evolution anzusehen, hilft nicht nur, den oft zitierten Ausspruch von Charles Eames: „Details sind keine Details. Sie machen das Produkt aus“ zu verstehen, sie sagt auch viel über die Verantwortung, die Herman Miller sowie das Büro und die Familie Eames auf Bitten der Eames' übernommen haben, nämlich dem unermüdlichen Bestreben der Designer, ihre Designs zu verbessern und zu verfeinern, gerecht zu werden.
Die Eames' waren in Materialfragen bekannt agnostisch und die Grundlagen für die Kunststoffschale, die wir heute bei ihren Stühlen kennen und lieben, wurden tatsächlich bereits Ende der 30er Jahre gelegt, als Charles Eames und Eero Saarinen anfingen, an der Cranbrook Academy of Art mit Stühlen aus gebogenem Sperrholz zu experimentieren. Saarinens Vater Eliel war Direktor von Cranbrook und Eero war damals Juniorpartner im Architekturbüro seines Vaters. Es ist wahrscheinlich, dass beide, Eames und Eero Saarinen, durch die Arbeit des finnischen Architekten Alvar Aalto beeinflusst waren, der Anfang der 30er Jahre an der Cranbrook Academy unterrichtete und bekannt war für seine Sperrholzmöbel. Die ersten Versuche von Eames und Saarinen, Sperrholz zu formen, wurden bei einem Stuhl umgesetzt, den sie für Eliel Saarinens Entwurf der Kleinhans Music Hall in Buffalo, NY 1939 konzipierten. Während dieser Stuhl noch zweidimensionale Biegungen hatte, gelang es ihnen bei ihrem Beitrag für den Wettbewerb des Museum of Modern Art für „Organic Design“ von1940, dreidimensionale Biegungen herzustellen. Sie gewannen den ersten Preis, der Stuhl wurde jedoch nur in sehr begrenzter Anzahl hergestellt und hatte nicht annähernd die gewünschte Qualität. Charles Eames hatte inzwischen Ray Kaiser, eine Studentin in Cranbrook, kennengelernt und geheiratet, und die beiden waren nach Venice in Kalifornien gezogen und hatten ihr Eames Office gegründet. Eero Saarinen verließ das Projekt, aber Charles und Ray Eames waren fest entschlossen, ein völlig neues Verfahren für das Biegen von Sperrholz zu komplizierten Formen zu entwickeln.
Charles und Ray Eames experimentierten weiter mit ihrer neuen Technik für die Formung von Sperrholz und so entstanden Tragbahren, leichte, stapelbare Beinschienen (1942) und ein Gleitersitz (1943) für die amerikanische Marine. Nach dem Krieg kehrten sie zu ihrem Projekt seriengefertigter Stühle zurück. Trotz all ihrer Bemühungen waren sie immer noch nicht in der Lage, eine Sperrholzschale aus einem Stück zu formen. Als Alternative bot sich schließlich ein Stuhl aus zwei getrennten Sperrholzteilen für Sitzfläche und Rückenlehne an, der spätere Eames Molded Plywood Stuhl (1946), der auch heute noch hergestellt wird und vom Time Magazine schließlich als „Bestes Design des Jahrhunderts“ gefeiert wurde. Zwei Jahre danach produzierten sie einen Stuhl mit einer einteiligen Shell aus gestanztem Metall für den internationalen Wettbewerb des Museum of Modern Art für „Low-Cost Furniture Design“. Ihr Stuhl kam auf den zweiten Platz, der mit Neopren beschichtete Prototyp war aber zu teuer in der Herstellung, deshalb begannen die Eames' sich mit anderen Materialien zu beschäftigen, wie etwa glasfaserverstärktem Kunststoff, ein Material, das in organische Formen gebracht und kostengünstig produziert werden konnte, aber bis dahin noch nicht für Verbrauchsgüter eingesetzt worden war.
Diese Version von 1950 wurde schließlich der erste seriengefertigte Kunststoffstuhl, war aber keineswegs das Ende der Evolution dieses Designs. Über die Jahre kamen verschiedene Optionen für Farbe und Höhe, Dämpferbrücken (die so genannten Shock Mounts), verschiedene Fußgestellvarianten und Polsterungen hinzu, so dass der Stuhl nicht nur leicht zu reproduzieren war, sondern auch individuell konfiguriert werden konnte. Auch die Fertigungsprozesse wurden genau überwacht und angepasst, aber Ende der 80er Jahre, fast ein Jahrzehnt nach Charles Eames' Tod 1978, stellten Ray Eames und Herman Miller schließlich die Glasfaserproduktion wegen der Auswirkungen auf die Umwelt in Frage. Bis zum Anfang der 90er Jahre stellte Herman Miller die Produktion daher ein. Nachdem viele Jahre lang nach umweltfreundlicheren Alternativen gesucht worden war, brachte das Unternehmen 2001 den Molded Plastic Shell Stuhl aus zu 100 % recycelbarem Polypropylen wieder heraus. Er basierte auf den Prototypen im Archiv des Eames Office, die Charles und Ray Eames in den 70er Jahren aus Kunststoff ohne Glasfaserverstärkung hergestellt hatten. 2013 setzte Herman Miller, wieder in Zusammenarbeit mit der Eames-Familie, die Vision der beiden Eames' eines Schalenstuhls mit einem neuen und sehr geeigneten Material um – geformtem Holz, was nun dank der Fortschritte in der 3D-Furniertechnik möglich geworden war. Und 2014 schließlich wurde der Shell Stuhl wieder aus nachhaltigem Fiberglas mit GREENGUARD Gold Zertifikat sowie in gepolsterter Form herausgebracht.
In Fortsetzung dessen, was die Eames' mit ihrem Film von 1970 „The Fiberglass Chairs: Something of How They Get the Way They Are“ begonnen haben, hat sich WHY den Glasfaserproduktionsprozess in unser Glasfaserfabrik in Ashtabula, Ohio, und in Herman Millers eigener Greenhouse-Fabrik in Zeeland, Michigan, angesehen und in zehn kurzen Videos festgehalten, die wir auf Instagram (zusammen mit den gif-Trailern unten) veröffentlichen werden. Sie zeigen, wie Herman Miller das Originaldesign und -ethos der Eames' ehrt, indem ein Höchstmaß an Qualität und Nachhaltigkeit für den Fertigungsprozess und die Fertigungsqualität angestrebt wird.
„Die Eames' waren in Materialfragen bekannt agnostisch und die Grundlagen für die Kunststoffschale, die wir heute bei ihren Stühlen kennen und lieben, wurden tatsächlich bereits Ende der 30er Jahre gelegt, als Charles Eames und Eero Saarinen anfingen, an der Cranbrook Academy of Art mit Stühlen aus gebogenem Sperrholz zu experimentieren.“
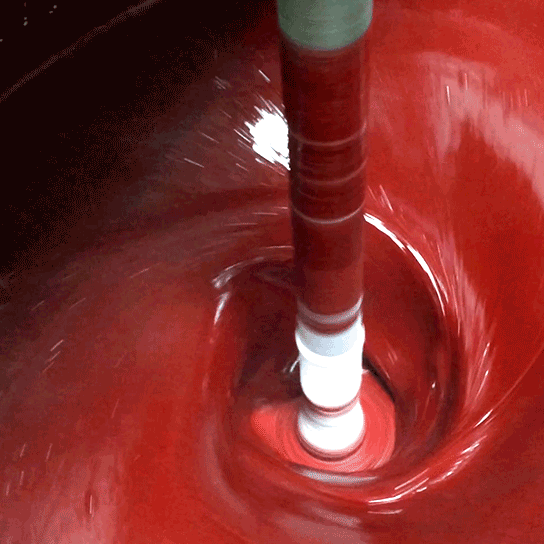
1. Gefärbtes Kunstharz wird in Bottichen gemischt
Durch den Einsatz von Technologien aus der Automobil- und Fertigungsindustrie zur Herstellung nichtdekorativer Funktionsteile kann das neue GFK-Harz von Herman Miller viele umwelttechnische Verbesserungen vorweisen. Es ist frei von Monomeren und wird ohne flüchtige organische Verbindungen (VOCs) oder gefährliche Luftschadstoffe hergestellt, so dass keine thermische Abluftreinigung erforderlich ist. Im Vergleich zur derzeitigen konventionellen Herstellung von GFK-Harz und zu den Harzen, die ursprünglich für die Stühle benutzt wurden, erzeugt das neue monomerfreie Kunstharz weniger Ozon und Luftschadstoffe, wodurch eine sicherere Arbeitsumgebung für die Mitarbeiter gewährleistet ist.
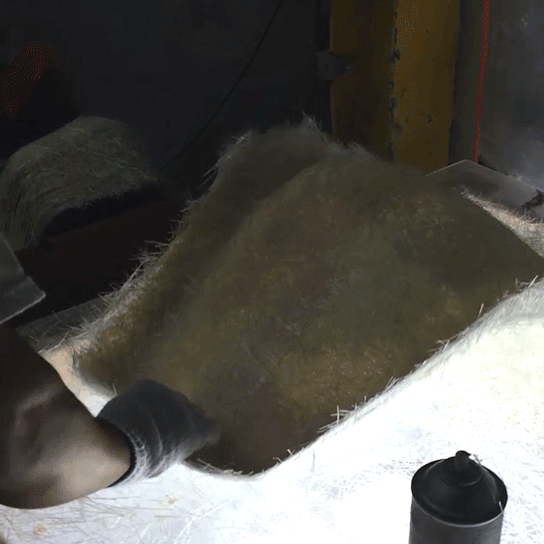
2. Formteile werden aus der CNC-Maschine genommen und geprüft
Zur Herstellung der Formteile für den neuen Shell Stuhl wird heute im Gegensatz zu früher ein Trockenverfahren eingesetzt. Bei diesem Verfahren werden die Glasfasern, von denen einige bei niedrigerer Temperatur schmelzen, von einer CNC-Maschine auf ein schalenförmiges Sieb geblasen. Durch ein Vakuum wird sichergestellt, dass lose Partikel zurückgehalten und nicht in die Luft geblasen werden und durch den „Nasskleber“ wie bei der herkömmlichen Fertigung gebunden werden. Dann wird Wärme aufgebracht, so dass ausreichend Fasern schmelzen und das Formteil zurückbleibt. Erst dann wird das Formteil von Menschen berührt, wenn es nämlich auf einem Lichttisch geprüft wird und die Kanten des Formteils mit einem Messer gesäubert und geglättet werden.

4. Das harzbeschichtete Formteil wird in eine Presse gegeben
Nachdem das Kunstharz gleichmäßig aufgetragen wurde, wird die Schale in eine Presse gesetzt, wo das harzbeschichtete Formteil Wärme und Druck ausgesetzt wird. Die Presse schneidet dann an der Kontur des Stuhls entlang, um vor dem Schleifen überschüssiges Glasfasermaterial zu entfernen.
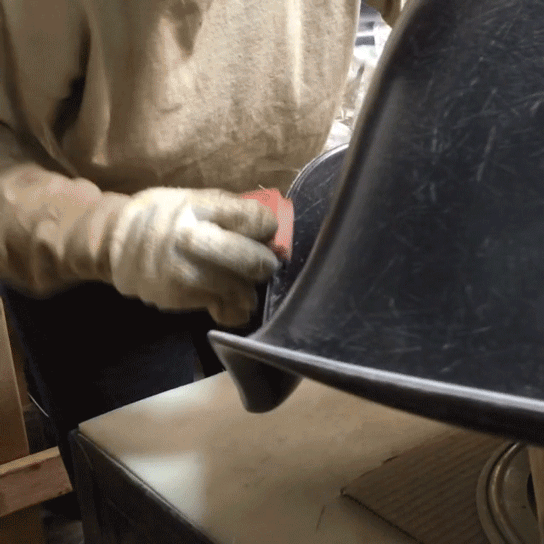
6. Die Kanten der Shell werden geschliffen
Die Kanten der Schale werden manuell mit Sandpapier geglättet und dann mit einer elektrischen Schleifmaschine feinbearbeitet. Danach wird der Stuhl abgewischt und in Folie gepackt. Er wird dann noch von einem weiteren Fabrikarbeiter geprüft, der noch einmal nach Fehlern sucht. Nach der Prüfung wird er zur Greenhouse-Fabrik von Henry Miller geschickt.
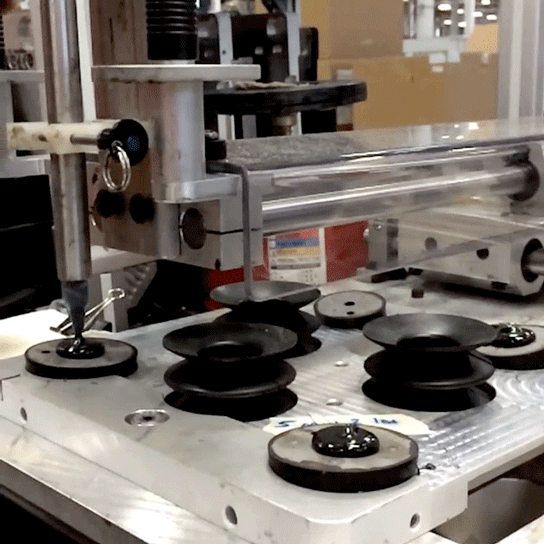
7. Die Dämpferbrücken werden unten auf die Schale aufgebracht
Die Unterseite der Schalen wird sorgfältig gereinigt, um die Dämpferbrücken sicher befestigen zu können. Eine Maschine trägt den Klebstoff auf die Dämpferbrücken auf, dann wird ein Tablett mit der frisch gereinigten Schale auf diese aufgesetzt. Die Schale mit den Dämpferbrücken bleibt dann zwei Tage auf einem Gestell, wo sie unter Druck getrocknet wird und der Kleber aushärtet.