イームズプラスチックシェルチェアの物語は、1950年にチャールズ&レイ・イームズ夫妻がこのアイコニックなデザインのチェアをハーマンミラーのために発表するよりも10年以上も前に始まりました。10年にわたってチェアが進化してきた道すじをたどると、よく引用されるチャールズ・イームズの「ディテールは単なるディテールに留まりません。ディテールがデザインを作るのです」という言葉の意味が、はっきりと見えて来ます。ハーマンミラー、Eames Office、そしてイームズファミリーには、常により良いものを目指して進み続けデザインを改善し続けるという、イームズ夫妻から託された責任が有ります。
イームズ夫妻は素材にとらわれないことで有名でした。現在広く知られ愛されているプラスチックシェルの原型は、実は1930年代後半にチャールズ・イームズとエーロ・サーリネンがクランブルック美術アカデミーで曲線的フォルムのプライウッド製シーティングの可能性を探り始めたときに芽生えたものなのです。当時チャールズは同アカデミーでデザイン科の学科長を務めていました。サーリネンの父エリエルはクランブルックの学長で、エーロはその父の設計事務所のジュニア・パートナーでした。イームズもエーロも、フィンランドの建築家アルヴァ・アアルトの作品に影響を受けていたようです。プライウッドを曲げて製作したファニチャーで知られていたアアルトは、1930年代初めにクランブルックで講義を行っていました。イームズとサーリネンがプライウッド成型チェアに取り組んだ最初の試みは、1939年にエリエルが設計したニューヨーク州バッファローのクラインハウス音楽ホールで実現しました。このチェアは平面的な曲線を持ったものでしたが、ニューヨーク近代美術館が1940年に開催した「オーガニックデザイン」展に出品したふたりの次の作品は、立体的な曲線を備えていました。このチェアでふたりは1位を獲得しましたが、製造されたのはごくわずかな数で、ふたりが真に望んだクオリティには達していませんでした。この時にはチャールズはクランブルックの学生だったレイ・カイザーと出会い、結婚して、カリフォルニア州のヴェニスに転居して自らの名を冠した事務所を構えていました。エーロ・サーリネンはプライウッドのプロジェクトを断念しましたが、イームズ夫妻はプライウッドを曲面成型するまったく新しい製造法を編み出そうと固く決意していたのです。
チャールズ&レイ・イームズ夫妻はプライウッドを成型する新しい技術で試行錯誤を重ね、その成果は米国海軍のための担架、軽量で積み重ねることのできる添え木(1942)、グライダー用シート(1943)などに実りました。第二次大戦後、2人は再び大量生産できるチェアに取り組みました。しかし、努力の甲斐なく座面と背もたれが一体型のプライウッドのシェルを作り出すことはできませんでした。その代わりに夫妻が見出した素晴らしい案が、背もたれと座面がそれぞれ独立した成型合板で作られているチェアです。これが現在に至るまで製造されているイームズプライウッドチェア(1946)となりました。このチェアは『タイム』誌の「Best Design of the Century(20世紀最高のデザイン)」にも選ばれています。その2年後、イームズ夫妻はニューヨーク近代美術館で行われた「International Competition for Low-Cost Furniture Design(低コストファニチャーデザイン国際コンペティション)」のために金属板をプレス加工した一体型シェルチェアを製作しました。このチェアはコンペティションの2位を獲得したものの、ネオプレンでコーティングした試作品は大量生産するには費用が高すぎたため、夫妻はファイバーグラスで補強されたプラスチックという新しい素材を模索し始めたのです。有機的な形状に成型することができ、生産上のコスト効率も良い素材ですが、当時はまだ消費財には使われていませんでした。
1950年に販売が開始されたこのチェアが、大量生産された最初のプラスチックチェアとなりました。しかし、デザインの進化はこれでおしまいではありませんでした。その後何年にもわたり、カラーや高さのオプション、ショックマウント、ベースのオプション、張地の選択肢などが次々と増え、生産しやすいだけではなく、カスタマイズの選択肢がきわめて高いチェアになっていきました。製造プロセスにも一貫した注意が注がれ、改良されてきています。チャールズが1978年に亡くなってからおよそ10年後の1980年代後半、レイ・イームズとハーマンミラーはファイバーグラス製造過程の環境への影響に懸念を抱くようになりました。1990年代初頭までに、ハーマンミラーはその製造を中止しました。その後、より持続可能性の高いソリューションを何年もかけて探った後、ハーマンミラーは100%リサイクル可能なポリプロピレン製のプラスチックシェルチェアを2001年に再発売しました。これは、1970年にチャールズ&レイ・イームズ夫妻がファイバーグラスを含まないプラスチックで作った、Eames Officeに保存されていた試作品を基にしたものです。2013年、再びイームズファミリーの協力を得て、ハーマンミラーはチャールズ&レイ・イームズ夫妻のシェルチェアを、新しい、そしてこのチェアにきわめてふさわしい素材、つまりウッドベニアで製造しました。これは最先端の3Dベニア技術により実現したものです。そして今年、持続可能性を高めGREENGARDのゴールド認定を受けたファイバーグラスで、ハーマンミラーはシェルチェアの製造販売を再開し、同時にファブリック張りのオプションも再開しました。
イームズ夫妻が作った1970年の映画「The Fiberglass Chairs:Something of How They Get the Way They Are(ファイバーグラスチェア:チェアができるまでのあれこれ)」を引き継ぐため、WHYではファイバーグラスチェアの製造工程を再訪しました。オハイオ州アシュタブラのファイバーグラス製造工場、そしてミシガン州ジーランドにあるハーマンミラーの自社施設Greenhouseのようすを、短い動画10本にして、2日間にわたってInstagramに順次アップしました(それぞれの動画のハイライトを収めたgifアニメも以下でご覧いただけます)。ハーマンミラーが製造行程と品質を最高レベルでかつ可能な限り持続可能性の高いものにし、イームズ夫妻のデザインと理念を尊重している様子をご覧いただけることでしょう。
“イームズ夫妻は素材にとらわれないことで有名でした。現在広く知られ、愛されているプラスチックシェルの原型は、実は1930年代後半にチャールズ・イームズとエーロ・サーリネンがCranbrook Academy of Artで曲線的フォルムのプライウッド製シーティングの可能性を探り始めたときに芽生えたものなのです。”
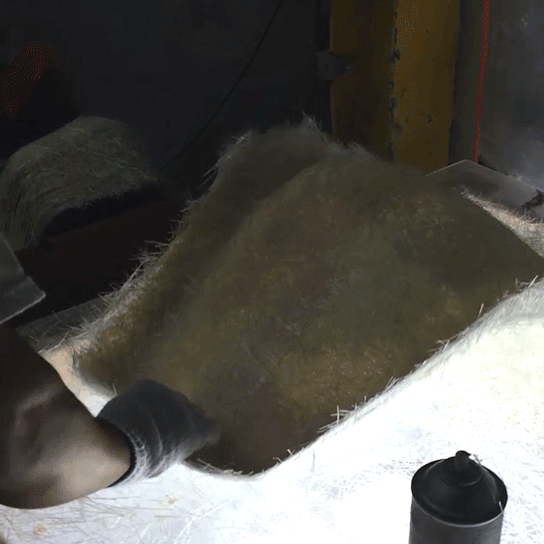
2.CNC装置からプリフォームを取り外して検品
新しいシェルチェアのプリフォームの製造には、従来の「湿式プロセス」に代わり「ドライバインダープロセス」が採用されています。「ドライバインダープロセス」では、CNC(コンピュータ制御)工作装置がシェルの形状をしたスクリーンにファイバーグラス繊維を吹き付けます。繊維の一部は低温で溶けます。この過程は真空で行われるため粒子が封じ込められ、従来の工程のように空気中に吹き飛ばされた粒子を接着剤に吸着する必要がありません。熱を加え充分な量の樹脂を溶かし、プリフォームのフォルムを保ちます。ここで初めて人の手が入ります。ライトテーブルの上で予成形品を検品し、ナイフを使ってプリフォームの縁をトリミングします。