Het verhaal van de plastic schelpstoel van Eames begon eigenlijk meer dan tien jaar vóór Charles en Rays debuut van hun nu iconische ontwerp voor Herman Miller in 1950. Het begrijpen van deze decennialange evolutie helpt niet alleen het door Charles vaak geciteerde - “De details zijn geen details. Ze maken het ontwerp” te begrijpen, het zegt ook veel over de verantwoordelijkheid die Herman Miller en de Eames Office en -familie hebben aangenomen op verzoek van Charles en Ray, om trouw te blijven aan de eindeloze wil van ontwerpers om hun ontwerpen te verbeteren en verfijnen.
Het echtpaar Eames was notoir materiaalagnostisch, en het eerste idee van de plastic kuip die we nu kennen en liefhebben is al eind jaren 30 ontstaan toen Charles en Eero Saarinen voor het eerst begonnen met de verkenning van multiplexstoelen in gekromde vorm bij Cranbrook Academy of Art, waar Charles werkte als het hoofd van de ontwerpafdeling. Saarinens vader Eliel was het hoofd van Cranbrook en Eero was junior vennoot bij zijn vaders architectenbureau. Het is waarschijnlijk dat het echtpaar Eames en Eero werden beïnvloed door het werk van de Finse architect Alvar Aalto, die begin jaren 30 had gedoceerd in Cranbrook en erg bekend was om zijn meubels van gebogen multiplex. Eames en Saarinens eerste poging tot het vormen van multiplex werd gerealiseerd in een stoelconcept voor Eliels ontwerp voor de Kleinhans Music Hall in Buffalo, New York, in 1939. Hoewel die stoel tweedimensionale krommingen had, had hun volgende ontwerp, een inzending voor de wedstrijd “Organic Design” van het Museum of Modern Art in 1940, driedimensionale krommingen. Hier wonnen ze de eerste prijs mee, maar het werd in een zeer beperkte oplage geproduceerd en helemaal niet volgens de door hun gewenste kwaliteit. Op dat moment was Charles in contact gekomen en getrouwd met Ray Kaiser, een student aan Cranbrook, en de twee verhuisden naar Venice, Californië om hun gelijknamige kantoor te openen. Eero stapte van het project af, maar Charles en Ray waren vastbesloten om een volledig nieuw proces te ontwerpen voor het vormen van multiplex in samengestelde vormen.
Charles en Ray bleven experimenteren met hun nieuwe techniek voor het buigen van multiplex en hun inspanningen leverden stretchers, lichtgewicht, stapelbare beenspalken (1942) en een stoeltje op voor een zweefvliegtuig (1943) voor de Amerikaanse marine. Nadat de oorlog was afgelopen, richtten ze zich weer op het concept van een massaproductiestoel. Ondanks hun beste inspanningen waren ze nog steeds niet in staat om een multiplexvorm met een enkele huls te produceren, maar belandden ze in plaats daarvan bij een interessant alternatief: een stoel die bestaat uit aparte gebogen multiplexpanelen voor de rugleuning en de zitting, wat uiteindelijk de Eames stoel van gevormd multiplex (1946) zou worden, die tot op de dag van vandaag in productie is en door het tijdschrift Times is benoemd tot “beste design van de eeuw”. Twee jaar later produceerden ze een stoel uit één vorm die uit metaal was gestanst voor de wedstrijd “International Competition for Low-Cost Furniture Design” van het Museum of Modern Art. Het verdiende de tweede plaats in de wedstrijd, maar het met neopreen gecoate prototype was te duur om in productie te nemen, dus begonnen Charles en Ray met het onderzoek van nieuwe materialen zoals plastic verstevigd met glasvezel, een materiaal dat in organische vormen kon worden gevormd en kosteneffectief geproduceerd kon worden, maar nog nooit was gebruikt in een consumentenproduct.
Het was deze iteratie - gelanceerd in 1950 - die later de eerste plastic massaproductiestoel werd, maar dat was niet het einde van de evolutie van het ontwerp. Door de jaren heen zijn de kleur- en hoogteopties, schokdempers, onderstelvariaties en stofferingskeuzes verdubbeld, wat de stoel niet alleen eenvoudig reproduceerbaar maakt, maar ook in hoge mate aanpasbaar. Fabricageprocessen worden ook nauwlettend gevolgd en aangepast en eind jaren 80, bijna een decennium na het overlijden van Charles in 1978, werden de gevolgen van glasvezelproductie voor het milieu onderzocht door Ray en Herman Miller. Rond de jaren 90 stopte Herman Miller de productie. Na jarenlang meer duurzame oplossingen te hebben verkend, herintroduceerde het bedrijf in 2001 de schelpstoel van gevormd plastic in 100% recyclebaar polypropyleen, op basis van prototypen in de archieven van de Eames Office die Charles en Ray hadden gemaakt met glasvezelvrij plastic in de jaren 70. In 2013, toen ze opnieuw met de Eames-familie werkten, realiseerde Herman Miller Charles en Ray’s visie voor de shell-stoel met een nieuw en heel toepasselijk materiaal - gebogen hout, dankzij de verbeteringen in de 3D-fineertechnologie. Dit jaar heeft het het bedrijf de schelpstoel opnieuw uitgebracht in zowel duurzaam geherformuleerd, GREENGUARD Gold Certified, gevormd glasvezel als met bekleding.
WHY gaat verder waar het echtpaar Eames stopte met hun film uit 1970, “The Fiberglass Chairs: Something of How They Get the Way They Are” en bezoekt het glasvezelproductieproces in onze glasvezelproductiefaciliteit in Ashtabula, Ohio en in Herman Millers eigen Greenhouse faciliteiten in Zeeland, Michigan. Dat doen we in tien overzichtelijke video’s die we gedurende twee dagen op Instagram zullen plaatsen (samen met de corresponderende GIF-trailers hieronder), waarbij we de manieren verkennen waarop Herman Miller het oorspronkelijke ontwerp en ethos van Eames verkent, door het fabricageproces en de kwaliteit zo goed en duurzaam mogelijk aan te sturen.
“Het echtpaar Eames was notoir materiaalagnostisch, en het eerste idee van de plastic kuip die we nu kennen en liefhebben is al eind jaren 30 ontstaan toen Charles en Eero Saarinen voor het eerst begonnen met de verkenning van multiplexstoelen in gekromde vorm bij Cranbrook Academy of Art.”
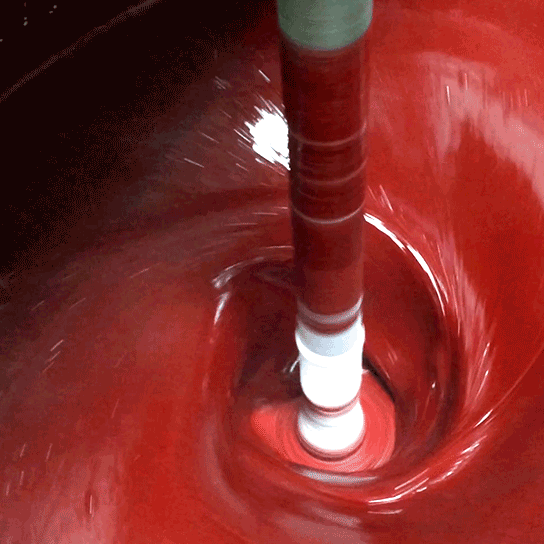
1. Gekleurde hars wordt in vaten gemengd
Door technologie te gebruiken die voornamelijk in de automobiel- en maakindustrieën wordt gebruikt om niet-cosmetische prestatieonderdelen te creëren, bevat Herman Millers nieuwe glasvezelhars vele verbeteringen ten opzichte van het milieu. Vrij van monomeren en verwerkt zonder VOC (volatiele organische componenten) of HAP-emissies (gevaarlijke luchtvervuilende stoffen), verwijdert deze hars de behoefte aan thermische oxidators. Vergeleken met de huidige conventionele glasvezelharsproductie en met de glasvezelharsen die werden gebruikt in de oorspronkelijke stoelen, produceert de nieuwe monomeervrije hars minder ozon en minder luchtvervuiling, wat leidt tot een veiliger werkomgeving voor werknemers.
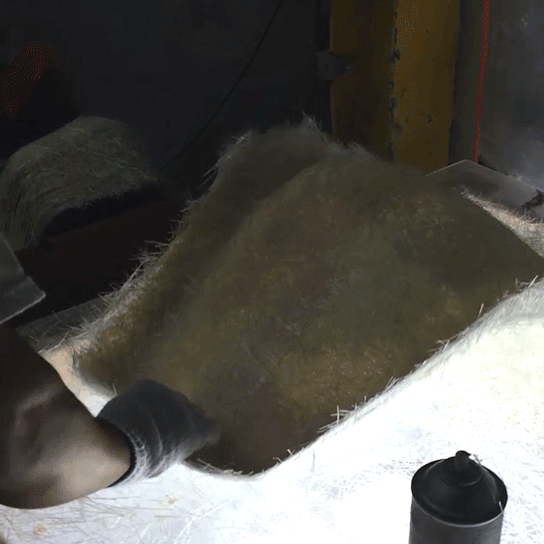
2. Preforms worden uit de CNC-machine gehaald en geïnspecteerd
Om preforms te maken voor de nieuwe schelpstoelen wordt een “droog bindingsproces” gebruikt, in tegenstelling tot het “natte proces” dat wordt gebruikt in conventionele glasvezelproductie. In een “droog bindingsproces” worden de glasvezeldraden, waarvan sommige bij een lagere temperatuur smelten, door een CNC-machine op een scherm geblazen in de vorm van een kuip; een vacuüm zorgt ervoor dat losse deeltjes worden afgevangen in plaats van weggeblazen te worden en opgevangen door de “natte lijm”, zoals bij conventionele productie. Daarna wordt warmte toegepast en smelten er voldoende draden om de vorm van de preform over te houden. Pas op dit moment raken menselijke handen de preform aan en alles wat er nog gedaan moet worden is een inspectie van de preform in een lichttafel en wat afwerken en schuren van de randen van de preform met een mes.

4. Een met hars gecoate preform wordt in een pers geplaatst
Nadat de hars gelijkmatig op de preform is aangebracht, wordt de kuip op de pers gezet, waar een combinatie van warmte en druk op de met hars gecoate preform wordt toegepast. De pers snijdt langs de contouren van de stoel om het teveel aan glasvezel vóór het schuren te elimineren.

5. De kuip wordt geïnspecteerd
Al het teveel aan preform dat nog aan de stoel hangt nadat het door de pers is afgesneden, wordt met de hand verwijderd en de kuip wordt uit de pers gehaald en met het blote oog geïnspecteerd en goedgekeurd door een fabriekswerker. Na elk gebruik wordt de pers gereinigd.
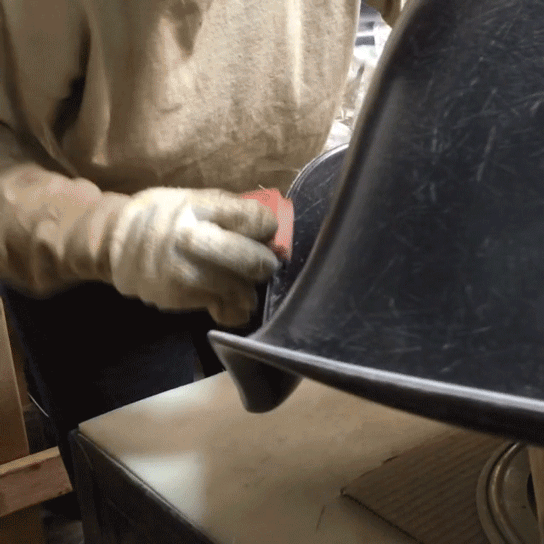
6. De kuipranden worden geschuurd
De randen van de kuip worden met de hand geschuurd en daarna afgewerkt met een elektrische schuurmachine. Daarna wordt de stoel schoongeveegd en verpakt. Vanaf hier wordt het nog één keer door een andere fabriekswerker geïnspecteerd die op imperfecties let. Nadat het is geslaagd voor de inspectie, wordt het naar de Greenhouse-vestiging van Herman Miller verzonden.
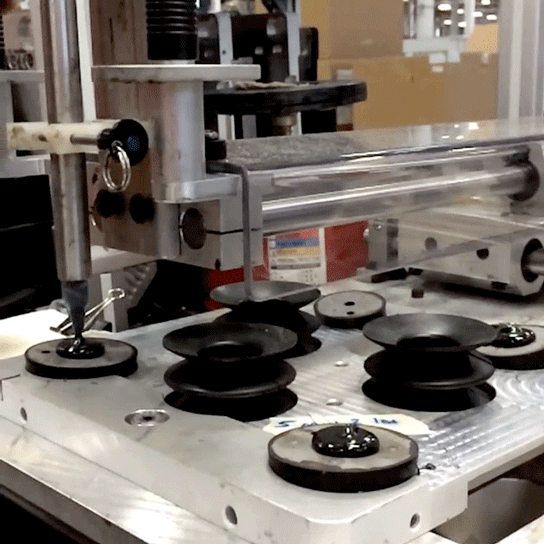
7. Schokdempers worden op het onderstel van de kuip aangebracht
Het onderstel van elke kuip wordt systematisch gereinigd om de schokdempers zo effectief mogelijk te lijmen. De lijm wordt door een machine op elke schokdemper aangebracht en een rek met de net gereinigde kuip wordt op de schokdempers geplaatst. De met schokdempers uitgeruste kuipen worden gedurende twee dagen op een persdroogrek geplaatst om uit te harden.

10. Bekleding aan de stoel bevestigd
Er wordt bekledingsschuim op de stoel bevestigd, waar de genaaide en geassembleerde bekleding overheen wordt geplaatst en wordt vastgezet door het J-kanaal (of randafwerking). Vanaf daar wordt het gestreken en in een andere pers geplaatst die warmte en druk toepast.