The story of the Eames Plastic Shell Chair really began more than ten years prior to Charles and Ray’s 1950 début of their now iconic design for Herman Miller. Understanding this decade-long evolution not only helps to shed light on Charles’ oft-quoted “The details are not the details. They make the design”; it says a lot about the responsibility Herman Miller and the Eames Office and family have assumed at Charles and Ray’s request, to stay true to the designers’ tireless drive to improve and refine their designs.
The Eameses were notoriously material agnostic, and the seeds of the plastic shell we know and love today were really planted in the late
Charles and Ray continued to experiment with their new technique for
Released in 1950, it was this iteration that went on to become the first mass-produced plastic chair, but it was not the end of the design’s evolution. Through the years,
Taking off where the Eames left off with their 1970 film, “The Fiberglass Chairs: Something of How They Get the Way They Are”, WHY revisits the fibreglass production process in our fibreglass manufacturing facility in Ashtabula, Ohio, and in Herman Miller’s own Greenhouse facilities in Zeeland, Michigan, in ten bite-sized videos that we’ll be releasing over the course of two days on Instagram (along with some corresponding gif trailers below). It will explore the ways in which Herman Miller is
“The Eameses were notoriously material agnostic, and the seeds of the plastic shell we know and love today were really planted in the late 1930s, when Charles and Eero Saarinen first began exploring plywood seating in curved forms at the Cranbrook Academy of Art.”
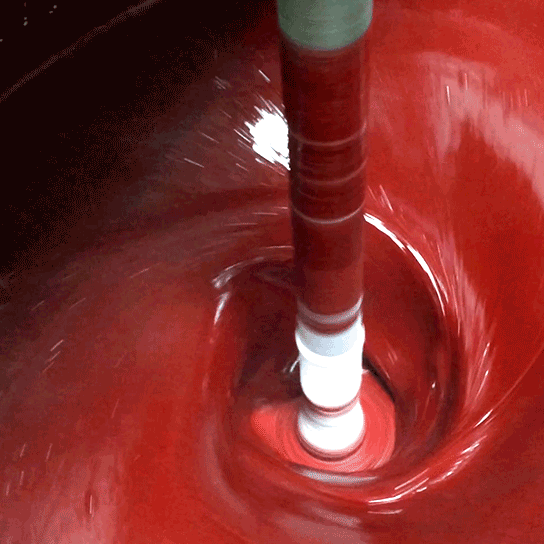
1. Coloured resin is mixed in vats
By employing technology used mainly in the automotive and manufacturing industries to create non-cosmetic performance parts, Herman Miller’s new fibreglass resin boasts many environmental improvements. Monomer-free and processed without VOC (volatile organic compounds) or HAP (hazardous air pollutants) emissions, this resin eliminates the need for thermal oxidisers. Compared to current conventional fibreglass resin production and to the fibreglass resins used in the original chairs, the new monomer-free resin produces less ozone and air pollution and results in a safer work environment for employees.
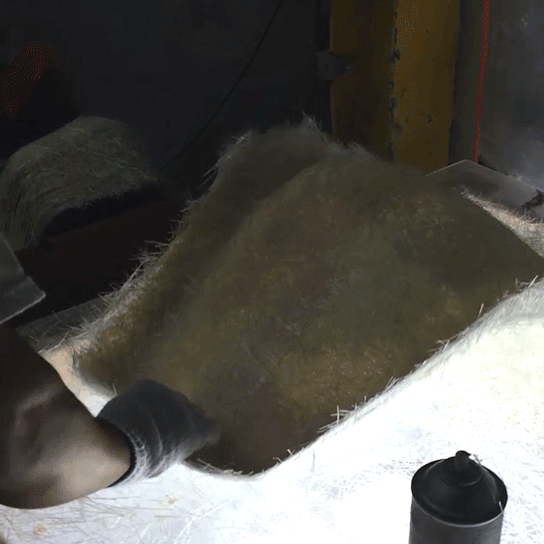
2. Preforms are removed from the CNC machine and inspected
To create preforms for the new Shell Chairs, a “dry binder process” is used as opposed to the “wet process” used in conventional

4. Resin-coated preform is placed in press
Once the resin has been evenly applied to the preform, the shell is moved onto the press, where a combination of heat and pressure are applied to the resin-coated preform. The press cuts along the contour of the chair to eliminate excess
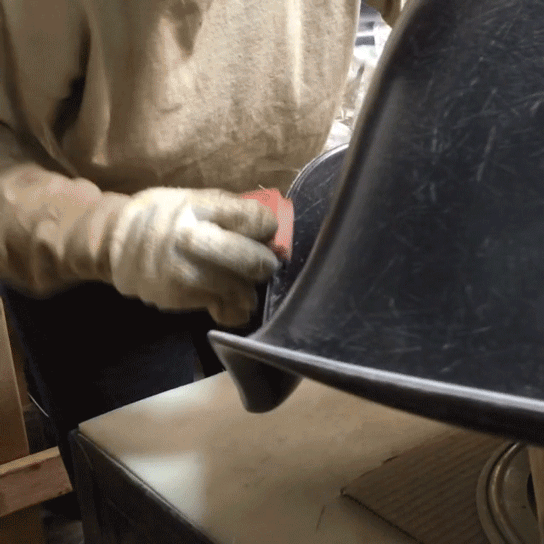
6. Shell edges are sanded
The edges of the shell are sanded manually and then finished with an electric sander. The chair is then wiped down and bagged. From here it’s inspected one more time by a different factory worker who is searching for imperfections. After it passes inspection, it is sent to the Herman Miller Greenhouse facility.
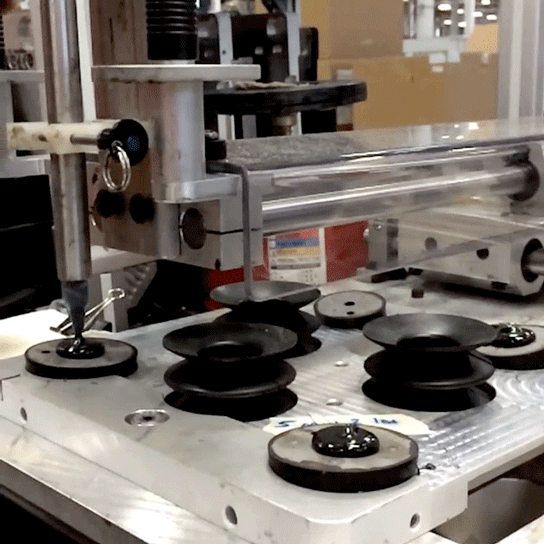
7. Shock mounts are applied to the base of the shell
The base of every shell is cleaned systematically in order to adhere to the shock mounts most effectively. Glue is applied to each shock mount by a machine, and a tray carrying the newly cleaned shell is set down on the shock mounts. The shock-mounted shells are set to cure on a