La storia delle sedute in plastica Eames Shell era iniziata oltre dieci anni prima del debutto di Charles e Ray nel 1950, con un design divenuto un'icona del catalogo Herman Miller. Comprendere questa evoluzione decennale non solo aiuta a far luce sulla citatissima frase di Charles: "I dettagli non sono dettagli. Sono una componente fondamentale del design", ma la dice lunga anche sulle responsabilità che Herman Miller, Eames Office e famiglia si sono assunte seguendo la filosofia di Charles e Ray, vale a dire restare fedeli all'instancabile ispirazione dei designer per consentire loro di migliorare e perfezionare i propri progetti.
Gli Eames erano noti per la sperimentazione dei materiali, e i semi che hanno portato al "guscio" di plastica che conosciamo e amiamo oggi furono piantati alla fine degli anni '30, quando Charles ed Eero Saarinen iniziano a esplorare la possibilità di realizzare sedili di compensato in forme curve presso la Cranbrook Academy of Art, dove Charles svolgeva il ruolo di responsabile del reparto di progettazione. Eliel, padre di Saarinen, era il direttore della Cranbrook Academy of Art, mentre Eero era un socio junior presso lo studio di architetti del padre. È probabile che sia Eames che Eero siano stati influenzati dal lavoro dell'architetto finlandese Alvar Aalto, che aveva insegnato a Cranbrook nei primi anni '30 ed era particolarmente noto per i suoi arredi in compensato curvato. Il primo tentativo di Eames e Saarinen per la modellazione del compensato è stato compiuto durante la creazione del concept per un sedia che Eliel aveva creato per la Kleinhans Music Hall di Buffalo (New York) nel 1939. Mentre quella sedia presentava una serie di curve bidimensionali, il loro design successivo, candidato al concorso “Organic Design” organizzato dal Museum of Modern Art nel 1940, presentava curve tridimensionali. Per questo design si aggiudicano il primo premio, ma questo fu prodotto in un numero limitato di pezzi e non si avvicinava ancora agli standard di qualità desiderati. Charles aveva già incontrato e sposato Ray Kaiser, una studentessa della Cranbrook Academy, e i due si erano trasferiti a Venice, in California, per aprire lo studio che porterà il loro nome. Eero abbandona il progetto, ma Charles e Ray erano determinati a scoprire un processo completamente nuovo per la sagomatura del compensato in curve composite.
Charles e Ray continuano a sperimentare con la loro nuova tecnica di sagomatura del compensato, e i loro sforzi si concretizzano con la creazione di una serie di barelle e tutori ortopedici impilabili in materiale leggero (1942) e un sedile per alianti (1943) per conto della marina militare statunitense. Alla fine della guerra, Charles e Ray tornano al concetto di produzione in serie. Nonostante gli sforzi compiuti, non erano ancora in grado di produrre una forma di compensato a guscio unico, ma giungono a una valida alternativa: una sedia composta da pannelli separati di compensato sagomato per lo schienale e il sedile, che sarebbe diventata la seduta in compensato sagomato Eames (1946), ancora oggi in produzione, che successivamente sarebbe stata eletta "Best Design of the Century" (migliore design del secolo) dalla rivista Time. Due anni più tardi, i due designer producono una seduta a singola scocca realizzata in metallo stampato per l'iniziativa "International Competition for Low-Cost Furniture Design" (concorso internazionale per il design di arredi dai prezzi contenuti) promossa dal Museum of Modern Art. La seduta si aggiudica il secondo posto, ma il prototipo rivestito in neoprene era troppo costoso da produrre, tanto che Charles e Ray iniziano a cercare nuovi materiali, come la plastica rinforzata in vetroresina, un materiale che poteva essere modellato in forme organiche e prodotto a un prezzo più conveniente, per quanto mai utilizzato su prodotti di consumo prima di allora.
Questa rivisitazione, uscita nel 1950, diventa la prima seduta in plastica prodotta in serie, senza tuttavia segnare un punto d'arresto per l'ulteriore evoluzione del design. Infatti, nel corso degli anni, alcune caratteristiche quali colore e opzioni altezza, supporti antivibrazioni, varianti della base e opzioni dell'imbottitura, sono raddoppiate, rendendo la seduta facilmente riproducibile e altamente personalizzabile. Anche i processi produttivi sono stati attentamente monitorati e modificati e, alla fine degli anni '80, quasi dieci anni dopo la morte di Charles nel 1978, Ray e Herman Miller cominciano a preoccuparsi delle implicazioni ambientali della produzione di vetroresina. Entro i primi anni '90, Herman Miller sospende la produzione della linea. Dopo anni trascorsi ad esplorare soluzioni più sostenibili, nel 2001 l'azienda reintroduce la seduta Shell in plastica sagomata, realizzata in polipropilene riciclabile al 100%, recuperando i prototipi sepolti negli archivi di Eames Office che Charles e Ray avevano realizzato in plastica non contenente vetroresina nel 1970. Nel 2013, collaborando di nuovo con la famiglia Eames, Herman Miller dà forma tangibile alla visione di Charles e Ray sul design della seduta Shell utilizzando un nuovo efficace materiale, il compensato sagomato, grazie ai progressi registrati nel settore delle tecnologie di impiallacciatura 3D. Quest'anno, l'azienda ha reintrodotto la seduta Shell in due versioni: una realizzata con una speciale vetroresina ecologica riformulata con certificazione GREENGUARD Gold, e una con imbottitura.
Riprendendo la storia da dove Eames l'aveva lasciata con il documentario del 1970, “The Fiberglass Chairs: Something of How They Get the Way They Are”, WHY rivisita il processo di produzione della vetroresina nel nostro impianto specializzato con sede ad Ashtabula, in Ohio, e presso gli impianti della Greenhouse di Herman Miller a Zeeland (Michigan), in dieci cortometraggi che saranno pubblicati entro due giorni su Instagram (insieme ad alcuni dei trailer gif riportati di seguito). I cortometraggi analizzano il modo in cui Herman Miller è riuscita a onorare il design originale e l'ethos di Eames, puntando a una produzione e a una qualità migliore e più sostenibile.
“Gli Eames erano notoriamente sperimentatori dei materiali, e i semi che hanno portato al "guscio" di plastica che conosciamo e amiamo oggi furono piantati alla fine degli anni '30, quando Charles ed Eero Saarinen iniziarono a esplorare la possibilità di realizzare sedili di compensato in forme curve presso la Cranbrook Academy of Art.”
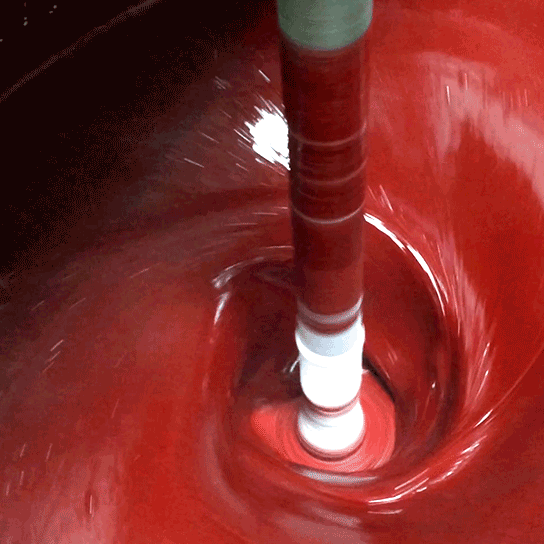
1. La resina colorata viene miscelata in una serie di tinozze
Impiegando una tecnologia utilizzata principalmente nell'industria automobilistica e manifatturiera per creare elementi prestazionali di tipo "non cosmetico", la nuova vetroresina di Herman Miller vanta numerosi miglioramenti ambientali. Priva di monomeri e trattata senza VOC (composti organici volatili) o emissioni di HAP (inquinanti atmosferici pericolosi), questa resina elimina la necessità di utilizzare ossidanti termici. Rispetto all'attuale produzione di vetroresina convenzionale e alle resine utilizzate sulle sedie originali, la nuova resina priva di monomeri produce meno ozono e inquinamento atmosferico e si traduce in un ambiente di lavoro più sicuro per i dipendenti.
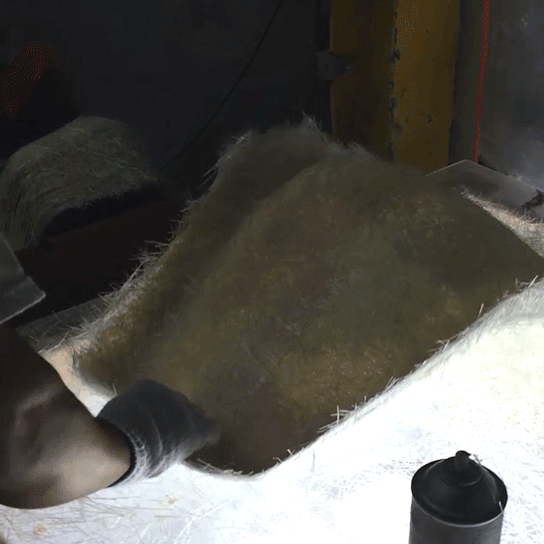
2. I preformati vengono rimossi dalla macchina CNC e ispezionati
Per creare preformati per le nuove sedute Shell, viene utilizzato un "processo di legatura a secco", anziché il "processo per via umida" utilizzato nella produzione di vetroresina convenzionale. In un "processo di legatura a secco" le fibre di vetro, alcune delle quali fondono a una temperatura più bassa, vengono soffiate da una macchina CNC su uno schermo a forma di guscio; un sistema di vuoto fa in modo che le particelle libere vengano trattenute anziché essere soffiate e catturate da uno strato di "colla umida", come accade nella produzione tradizionale. A questo punto si procede al riscaldamento fino a sciogliere un numero di fibre sufficiente per conferire al preformato una forma stabile e duratura. È solo a questo punto che il preformato viene lavorato manualmente, e le uniche operazioni richieste sono la sua ispezione su un tavolo leggero e l'eventuale smussatura o raschiatura dei bordi con un coltello.

3. La resina viene applicata al preformato
Il preformato in vetroresina viene collocato in un sostegno a "culla". Gli operatori procedono alla pesatura della resina per accertarsi che le quantità siano corrette, per poi versarla sul preformato di vetroresina, applicando il rivestimento e levigando la superficie del guscio in maniera sistematica e precisa tramite un utensile manuale.

4. Il preformato rivestito di resina viene collocato nella pressa
Una volta che la resina è stata uniformemente applicata al preformato, il guscio viene trasferito sulla pressa, e qui il preformato rivestito è soggetto all'applicazione di calore e pressione. La pressa taglia seguendo il profilo della sedia per eliminare la vetroresina in eccesso prima della levigatura.

5. Il guscio viene ispezionato
Il preformato in eccesso che rimane attaccato alla sedia dopo essere stato tagliato dalla pressa viene rimosso manualmente. A questo punto, il guscio viene estratto dalla pressa, ispezionato visivamente e approvato dall'operatore. La pressa viene pulita dopo ogni utilizzo.
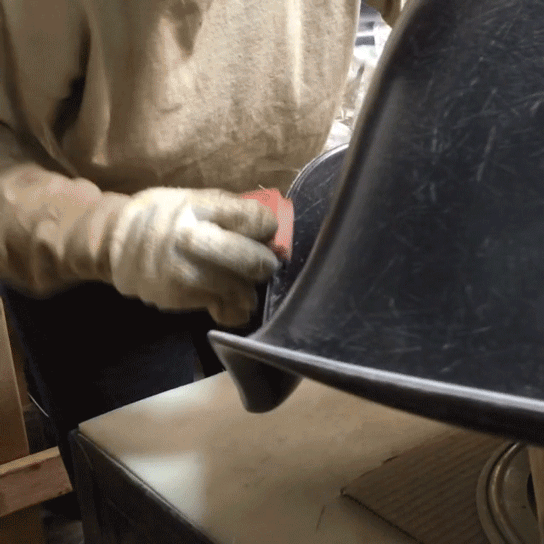
6. Il profilo della seduta Shell è soggetto a levigatura
I bordi del guscio vengono levigati a mano e poi rifiniti con una levigatrice elettrica. La sedia viene infine pulita e rivestita. A questo punto, la sedia viene ispezionata un'ultima volta da un altro operaio, che ha il compito di rilevare la presenza di eventuali imperfezioni. Dopo l'ispezione, viene inviata al centro Greenhouse di Herman Miller.
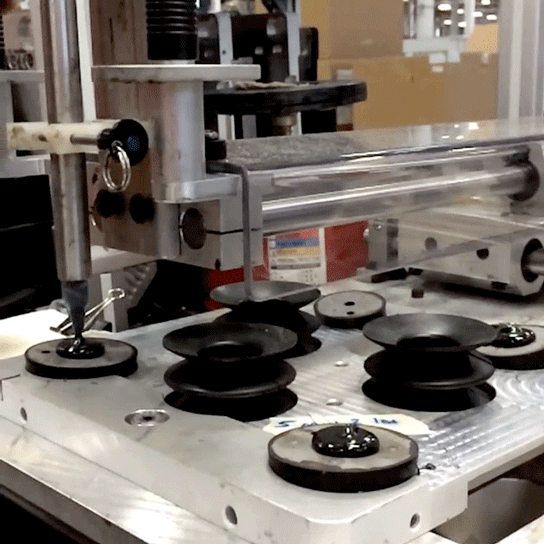
7. Si procede all'applicazione dei supporti antivibrazioni alla base del guscio
La base di ogni guscio viene pulita sistematicamente, in modo che possa aderire meglio ai supporti antivibrazioni. L'adesivo viene applicato a ciascun supporto antivibrazioni tramite un'apposita macchina, e un vassoio che trasporta il guscio appena pulito viene collocato sui supporti antivibrazioni. I gusci con supporti antivibrazioni vengono lasciati a riposo per due giorni su un telaio essiccatore pressurizzato.
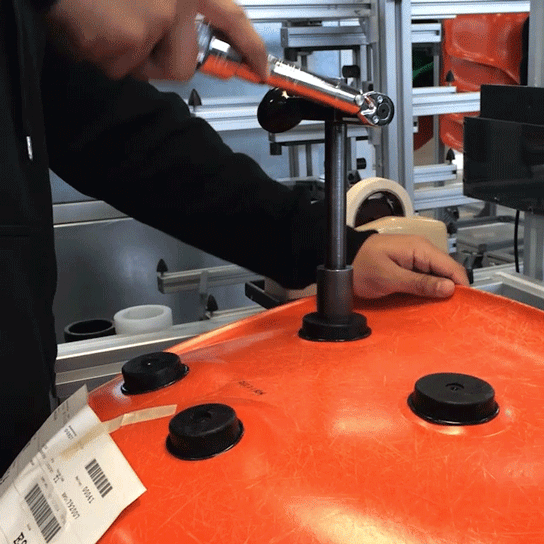
8. I dispositivi antivibrazioni vengono serrati e collaudati
I gusci con supporti antivibrazioni incorporati vengono rimossi dal telaio essiccatore ai fini del collaudo e dell'ispezione. Ogni supporto antivibrazioni viene serrato manualmente e, se supera il controllo, il guscio viene approvato definitivamente dallo stabilimento di produzione.

10. L'imbottitura viene fissata alla sedia
L'imbottitura in schiuma viene fissata alla sedia, sulla quale l'imbottitura cucita e assemblata viene applicata e fissata in corrispondenza del raccordo scanalato a "J" (o della bordatura perimetrale). A questo punto, l'imbottitura viene stirata e collocata su un'altra pressa che applica calore e pressione.